Year 2024
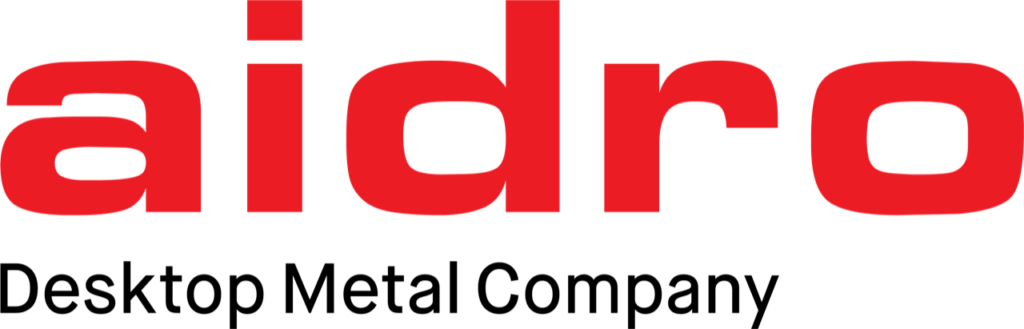
AIDRO presents ATILIUS Project
In collaboration with Kyklos 4.0, T4i Technology for Propulsion and Innovation, Optimad
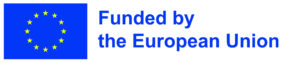
The ATILIUS project goal is the design, manufacturing, and testing of the fluidic subsystem of REGULUS-50-I2, a space plasma thruster for small satellites and CubeSats. The new ATILIUS design will enhance the efficiency of operations, and printability, lowering the environmental impact by using powders produced from scrap.
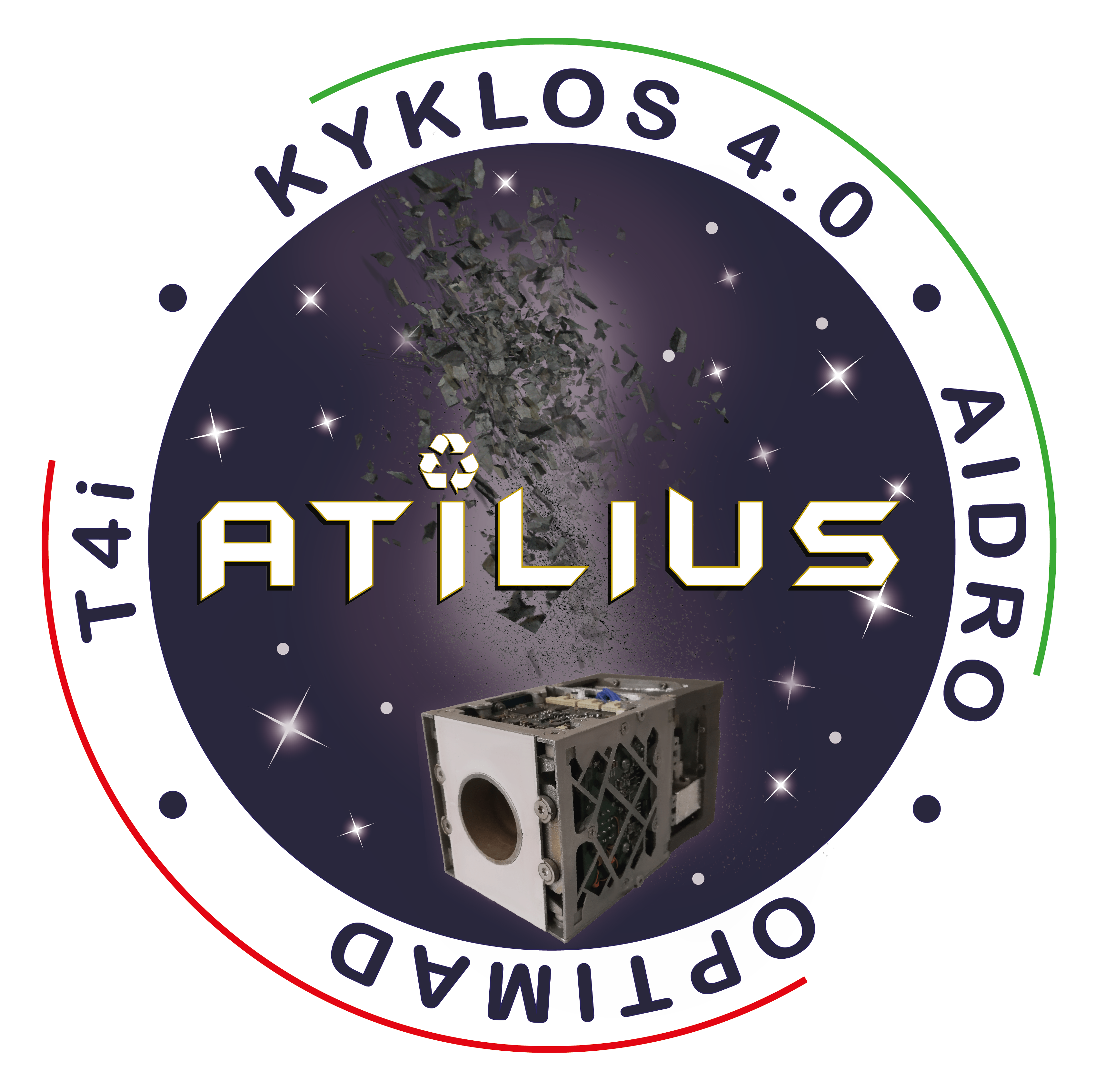
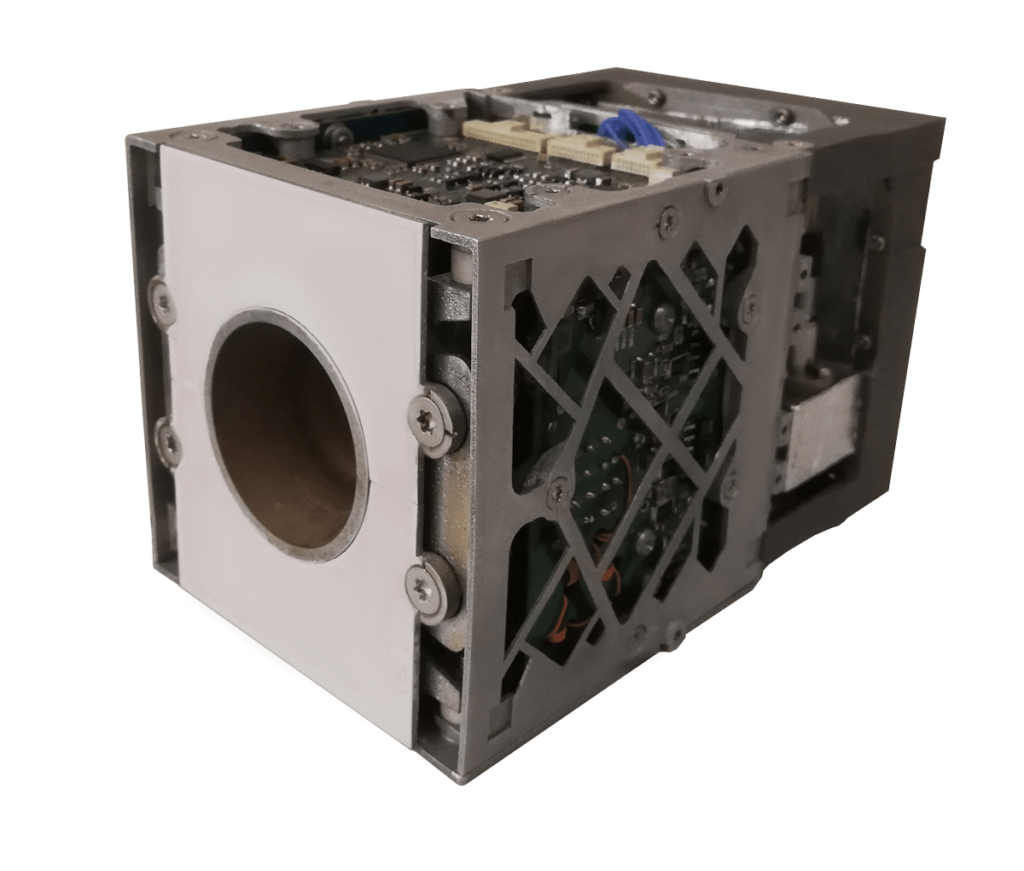
The design of ATILIUS is non-trivial, especially from a material point of view. In fact, REGULUS-50-I2 is a plasma thruster that uses iodine as propellant. Iodine is a chemically reactive element that tends to corrode several commonly used materials. For this reason, the material of which the fluidic subsystem is composed has been carefully evaluated.
Among others, superalloys such as Inconel are the most suitable. Inconel is an expensive and difficult to shape material, with a high rate of failure when machined. In order to decrease the production waste related to the manufacturing of the ATILIUS system, the powders used for 3D printing come from scrap and discarded pieces and parts. By doing so, the cost of the system will decrease, as well as the environmental impact of the finished product, in a recycling-oriented approach. This approach will ensure the circularity of the manufacturing process, that will be carefully monitored and measured throughout the entire project.
The ATILIUS project tackles several common problems in different fields.
First, the corrosive nature of iodine drove the material choice and, consequently, the processes. The lessons learnt during ATILIUS in machining and 3D printing corrosive-resistant material will be beneficial for applications that use chemically reactive compounds as iodine.
Moreover, the ATILIUS subsystem will be mounted on satellites, so the requirements in terms of volume, weight and mechanical robustness are stringent.
The design and manufacturing processes resulting from this project will pave the way for guidelines and good practices in the manufacturing of space qualified components.
Moreover, the heat exchange and the evaporation of the solid iodine will be analysed, modelled, and deeply studied with a dedicated numerical tool that will be developed during the ATILIUS project in order to enhance the efficiency of the fluidic subsystem. This numerical tool can be applied to different processes that involve phase changing materials to increase efficiency (e.g., heat exchanger, evaporator, etc.).
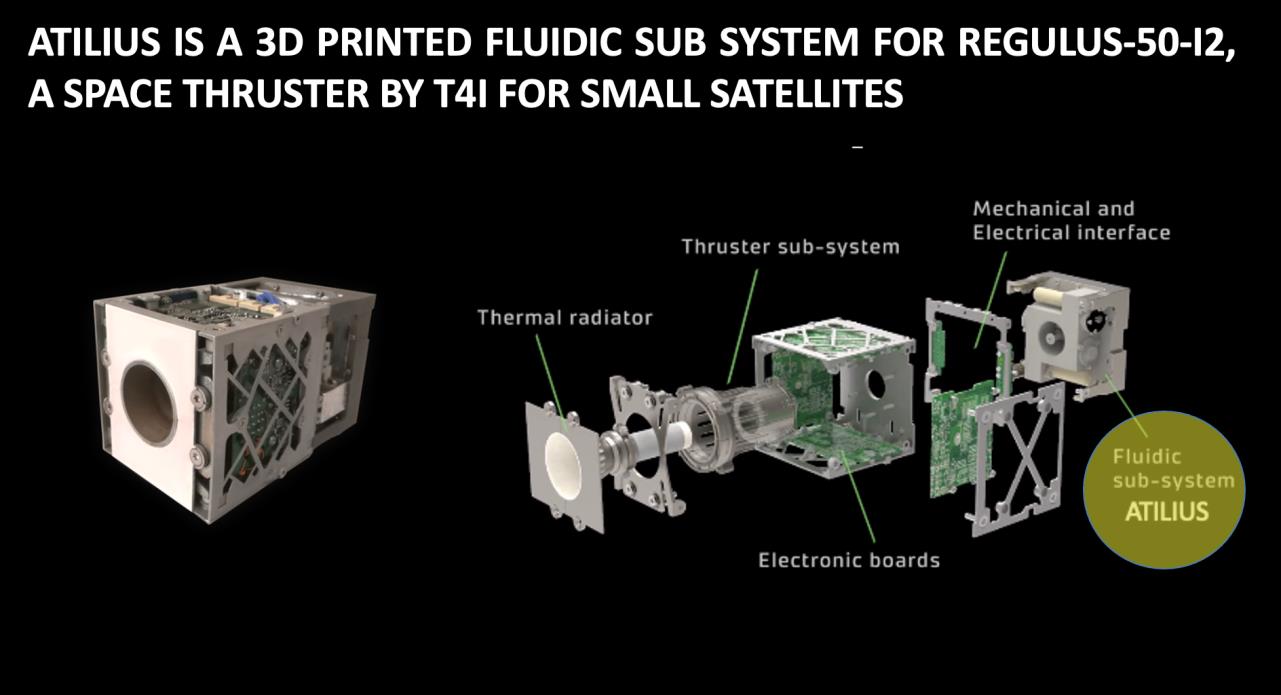
Making an established process more circular is often non-trivial.
First, what works is rarely changed to make it work better or in a more sustainable way.
Second, it is not always possible to change or adjust a specific design or process that is already optimised for means other than sustainability and circularity. However, sustainability of products and manufacturing processes is becoming urgent to decrease the environmental impact of our lives. In this framework, engineers and designers should design for recycling from a very early stage. This holds true for both products and processes. More specifically, the design of a product or process should take into considerations the 5 Rs of circular economy (i.e., refuse, reduce, reuse, repurpose, and recycle) from the beginning of the designing phase, by identifying shapes, materials, processes, and machining that is easy to recycle at the end of the product life and that are capable of reducing waste and pollution. Thus, the design-for-recycling approach should be included in the design process as a routine method, not considered as a nice to have.
Leave A Comment